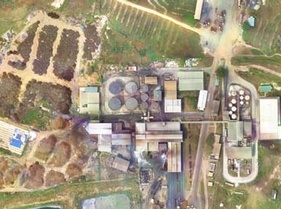
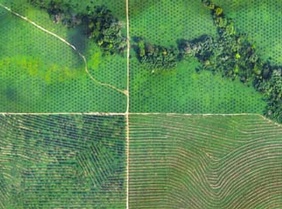
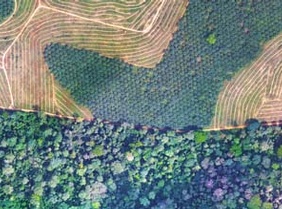
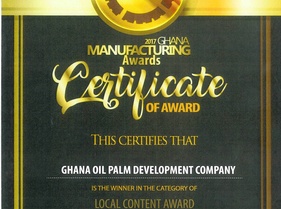
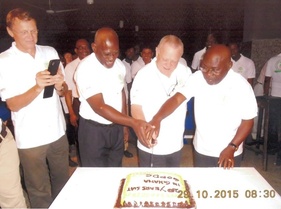
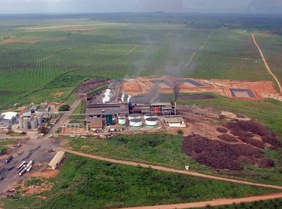

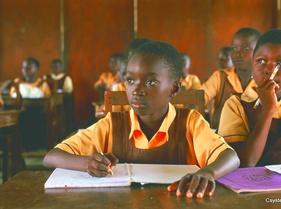
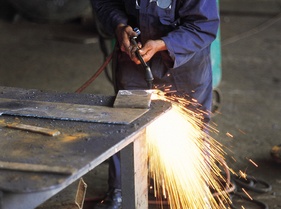
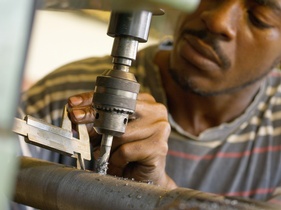

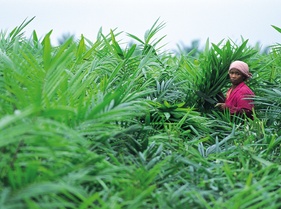
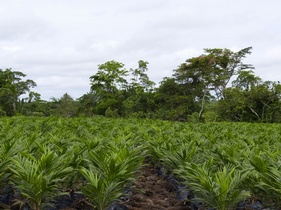
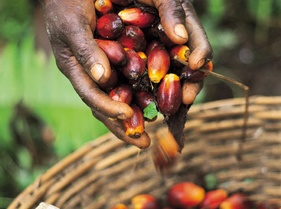
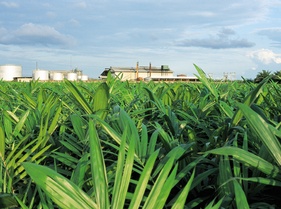
Our industrial facilities include:
In the refinery and fractionation plant, the crude palm oil (CPO) and palm kernel oil (PKO) is refined, bleached and deodorized (RBD) which will result in a bland product called RBDO or RBD PKO. This product can be sold as such but it can also be fractionated into olein (liquid) and stearin (solid). The olein is sold as cooking oil whilst stearin is used in many products such as bakery goods, margarines, quality soaps, maggi cubes, biscuits, milk, ice cream etc.
GOPDC was lucky to find in the vicinity of the mill two new borehole sites which provide together 45 m3 water per hour. This water is suitable for drinking but not automatically suitable for use in the boilers. In fact, the water from the boreholes needs to go through a series of treatments to become usable in the boilers. Therefore GOPDC has invested in a specialized water treatment plant. The equipments come from Infilco (a member of the Suez group) in France. The foundations for the water treatment plant were done by KOK and the building was assembled by Amitaab Ltd.
The scope of supply is a sand filter capable of filtering 35 m3 of raw water per hour, a duplex demineralization plant capable of treating 30 m3 of filtered water per hour, a water softener of 10 m3 per hour and a thermal deaerator for 30 tons of water per hour.
The water treatment plant was commissioned in May 2007.
In order to be able to cope with the increased processing capacity of the mill, the steam and power demands of the new refinery and fractionation plant, the rising costs of electricity and fossil fuels, GOPDC invested in a 30 MT/hour boiler with 2.5 MW turbine.
The new boiler produces 30 tons of superheated steam per hour, which runs a steam turbine to generate enough electricity to serve the mill, refinery/fractionation plant and the estate.
GOPDC produces huge amounts of organic waste (like empty fruit bunches, fibres and nut shells), which are burned as fuel in the boiler.
This project is a joint engineering project between Siat, CIRAD and Vyncke.
The refined and fractionated products need to be stored. Therefore, GOPDC has built a state of the art tank farm of 14 tanks. The current capacity of this tank farm is 6,000 tonnes.
The tanks are constructed in stainless steel to ensure optimal quality storage. Since refined and fractionated products have a shelf life which is much shorter than the crude products, additional care is taken of the products to keep the quality permanently to our customers’ specifications. When filling the tanks, nitrogen is injected to push away air (oxygen) to stop the natural oxidation of the goods. Stirrers are placed to homogenize the product on a permanent basis. Scanners and temperature probes are installed to check the stocks and to improve the traceability of the products.
2 weigh bridges are available to improve customer services, as well as an inox pipeline system towards the harbour in order to make the whole transfer of oil ‘carbon steel free’ .
With the installation of the palm kernel cake pellet plant at its Kwae Estate, GOPDC becomes the first company in West Africa to produce palm kernel cake pellets (PKCP). This is a ready product and a reasonably good economic feed for livestock, both for fattening and supplementary feeding. The pellets have a very high protein content needed for healthy growth of livestock.
The plant, of European origin, produces pellets of average size of 6 mm diameter and has a production and bagging capacity of 2000 kg/hr and 40 bags of 50 kg/hr respectively.
GOPDC Palm Kernel Cake Pellets -
7. Biomethanation plant.
One of the components of the CDM Emission Reductions Purchase Agreement related to Ghana Oil Palm Methane Recovering and Fuel-Switch Project (see ‘Environmental commitment’) is the installation of the biomethanation plant.
The biomethanation plant is made up of 4 main sections:
• The Bio-conversion Plant (bioreactors, entrance chambers and hydraulic tanks)
• The Digested Sludge Processing/Pasteurization/Stabilization Plant (solar pasteurizer)
• The Bio-fuel gas processing and Storage Plant (gas holders/scrubbers, compressors and gas reservoirs)
• In-Plant Waste Water Treatment Plant
An anaerobic digestion process will take place in the bioreactors which will result in two products: biogas (60 % methane, 40% carbon dioxide) and digested sludge.